There are 2 Lisas behind Azur (Favreau and Guedel-Dolle) but, on this occasion, it was Lisa Favreau whom Igor had a video chat with in April 2020.
The sun-filled images that accompany this interview have been taken by Andreas Lumineau (campaign photos), Pierre Girardin (lookbook photos), David Luraschi (portrait), Pierre Girardin (necklaces) and Azur (rest of images).
Is ‘transparency’ the latest buzzword in the fashion industry? We read about brands wanting to be transparent all the time but, let’s be honest, how much information is actually communicated to the customer?
It’s very rare to find a fashion label that has no problem in talking about its practices. Whether it’s hiding some dodgy supply chain processes or not wanting to disclosure certain information that could benefit its competitors, you normally won’t get the full story.
Azur is an exception. The Marseille-based brand, founded in 2019 by Lisa Favreau and Lisa Guedel-Dolle, wants its customers to know exactly how their garments have been produced. From the pattern makers to the dyers — and even the threads and buttons manufacturers — you just simply have to visit the brand’s website to access all these valuable details.
This honesty and the intention of offering something meaningful to their customers — created under many constraints — is also reflected in the conversation that follows.
Igor Termenón
Lisa Favreau
How did you and Lisa meet?
Lisa and I met in 2016 in Paris. She studied graphic design at ECAL in Lausanne, Switzerland, and I studied textiles in Paris. I was working as a freelance set designer, and Lisa was working as an art director and graphic designer when we met through common friends.
Even if we liked our jobs, we thought there was no meaning in them. We wanted to do something creative, but also more meaningful and representative of our beliefs. That’s how we started thinking about a project in which we could use our creative skills and energy for a more positive purpose.
Even if we liked our jobs, we thought there was no meaning in them.
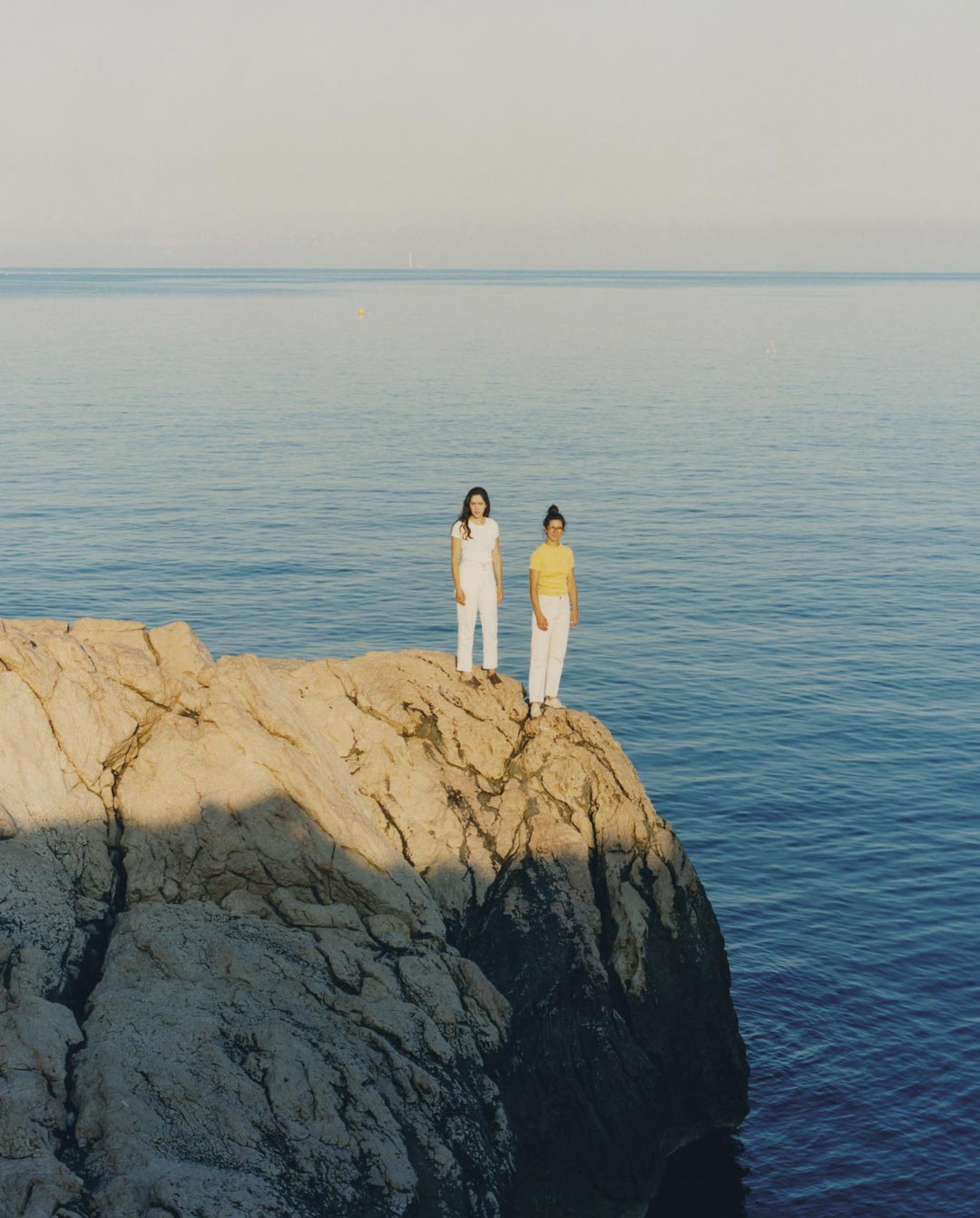
So, you were just thinking about different things you could do together?
At that time, we didn’t really know what was going to come out of it, but there was first and foremost a strong desire to change the way we were working and creating, to move towards more sustainable practices.
How did you get to the idea of making clothes and starting Azur?
Making truly ethical and eco-conscious clothing ended by being the most challenging of all the ideas we had. It also made sense, as we wanted to build a project that involved a lot of different people doing crafts — both professionals and non-professionals.
Furthermore, it was our idea to see clothing as an object independent from the codes of the fashion industry. Having a particular interest in plants, it was also a way for us to experiment with natural dyes.
When you started thinking about the pieces you wanted to produce, did you have a clear idea of what you wanted to make?
We initiated this project with the aim of offering a range of clothing that is rigorously clean and traceable, beyond what we think has been done so far. Garments in which each step of the manufacturing process is fundamentally respectful of the environment and individuals.
All of these constraints determined and affected many of the final designs.
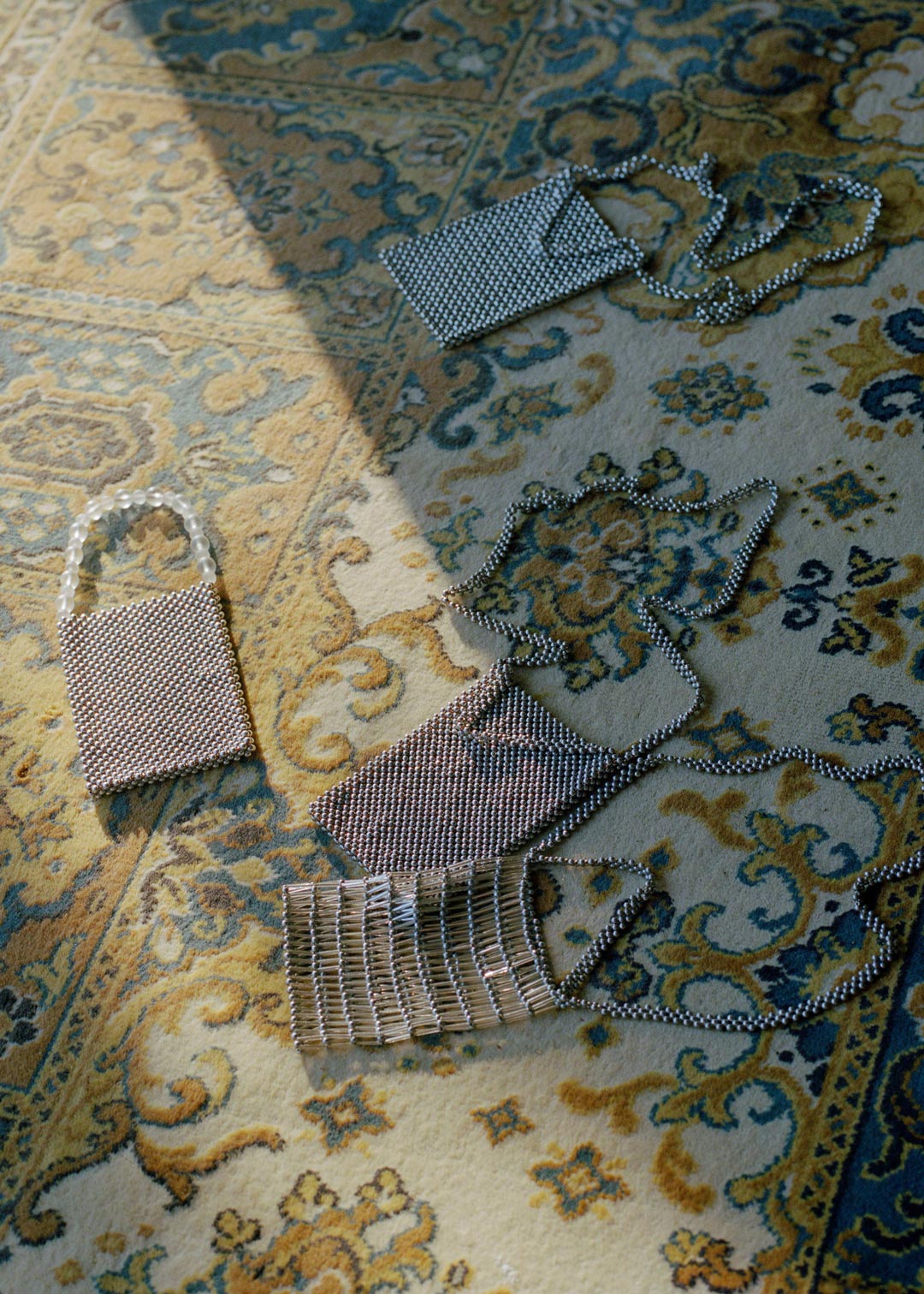
At the beginning we wanted to use natural fabrics that were 100% made in France, but we couldn’t find something that was manufactured from A to Z here1, so we decided to start looking for antique fabric, which have almost no environmental impact and their great quality is incomparable to what is done today.
Our main objective was to create unisex pieces and clothes you can wear everyday, and don’t fall out of fashion.
We wanted to do something very traceable and transparent, so all the constraints we had during the process determined and affected the final designs.
That’s really interesting. You had all these limitations that ended up giving shape to your designs. Sometimes, fashion is the complete opposite.
We were at Première Vision trade show in Paris, we saw all these fabrics and we thought, “wow, without all the constraints we chose for the brand, this is what we could make”. But in the end, we realised that the restrictions and limitations we imposed ourselves also create a certain framework that allows us to be creative. In the end it is a challenge for us to find new solutions through these limitations.
One thing I particularly love about your website is the care instructions. You provide detailed advice and use this quote: “Love your garment the way it is and the way it will evolve with you over time”. This is something that it’s finally starting to happen more often. Brands offering repair services and making customers understand that the pieces they buy are designed to be worn for a long time.
Our garments are more expensive than regular clothes, and we want to offer care instructions and repair services2 so they can last for a long time. In our opinion this goes along with the idea of making things in a sustainable way.
Our parents used to say that, when they were kids, they had just one pair of shoes that they would take to get repaired. We like this idea of looking back to the past and seeing how things were done. Let’s say you have a jumper and it has a hole in it, you can fix it instead of throwing it away.
We work with a seamstress — a super woman named Pauline — and she, for example, decided to make the hem of the dresses a little bit longer inside, so they could be worn by different people over time, and adjusted to their height.
Our parents used to say that, when they were kids, they had just one pair of shoes that they would take to get repaired. We like this idea of looking back to the past and seeing how things were done.
Can you tell me more about the different plant-based dyes you use and the processes?
We worked using two different techniques: a hot and a cold dyeing method.
The khaki, the brick and the light pink fabrics were dyed in Brussels in collaboration with a professional dyer using different plant extracts. It’s really an artisanal process close to the way of making tea but on a larger scale. Powdered dried leaves or plant extracts are put into a big pot with boiling water. Three to six meters of the fabric are then immersed — the equivalent of one or two garments — and have to be stirred for around 1 hour. To get certain shades, the fabric has to be prepared before, with a mordant — it’s a solution in which the fabric have to be soaked before the dyeing bath. That’s why it’s a long and artisanal process to obtain these colours.
Our blue pieces have been done with another process in Aix-en-Provence obtained with an indigo dye technique. In this case, the pieces have been garment dyed, which means that the garment is sewn before the dyeing bath. We used a white cotton thread and buttons made of natural corozo3. Because they are natural too, they are dyed along with the fabric. Each piece is immersed in the tank one by one several times — 5 times in our case — in order to yield a deep and lasting colour. The piece comes out in a greenish colour and, when it reacts with the oxygen of the air, turns into this particular blue shade.
Indigo is an organic dye derived from Indigofera plants. It is among the oldest dyes to be used for textile dyeing and printing, the process we follow is pretty much the same as was the one used 2000 years ago.
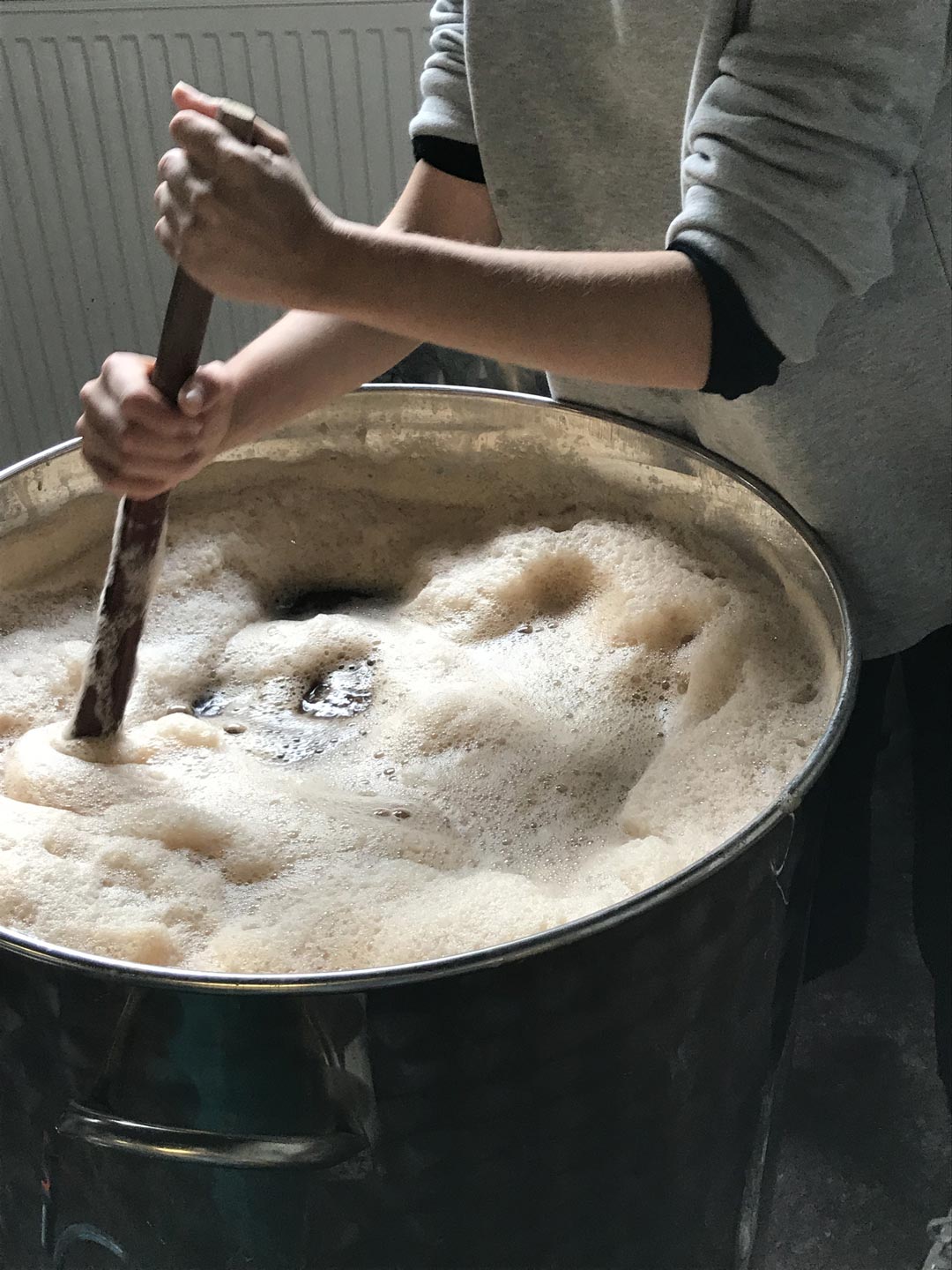
Right before the lockdown, we moved into a new space and we’re gonna set up a dyeing workshop. This way, we’ll be able to experiment more with our fabrics, get more freedom and be even more local in the process.
Your clothes are made on demand, so I guess this also makes sense in terms of speeding up the process a little bit.
Exactly. We dyed 10 metres of fabric in each colour and the pieces are made on demand but, from now on, it’s gonna be easier. We will also be able to dye the garments directly, as in the process with the indigo.
Right before the lockdown, we moved into a new space and we’re gonna set up a dyeing workshop. This way, we’ll be able to experiment more with our fabrics, get more freedom and be even more local in the process.
The made on demand model is really interesting, especially when you think about how we’re currently so used to having everything we want immediately. I think that waiting for something adds a little bit more value to it. What’s the average delivery time for your pieces?
It’s around 2 weeks. We didn’t want it to take a long time because, as you said, everybody wants everything immediately. Most of our customers understand it, so it’s not a problem.
And, you don’t have any stock at all?
No, we just have the fabrics that we dyed last spring in Brussels. And we also have lots of fabrics, buttons and embroideries that we didn’t use in the collection, which we source in France online (mainly from eBay and leboncoin4) and offline. We are constantly hunting for ancient fabrics and supplies, and our collection is slowly growing and serves as a pool of references and inspiration for us.
We’ve talked about some of the craftspeople behind Azur, is there anyone missing?
Actually, we haven’t talked about the two craftswomen behind our pleated silk pieces.
Last Spring we had the idea — that finally didn’t happen — of making beaded embroideries on shoes. Looking for embroiderers in Marseille, that’s how we met these two sisters and ended up in their family workshop — the embroidery didn’t work out, but we discovered that they were also pleaters.
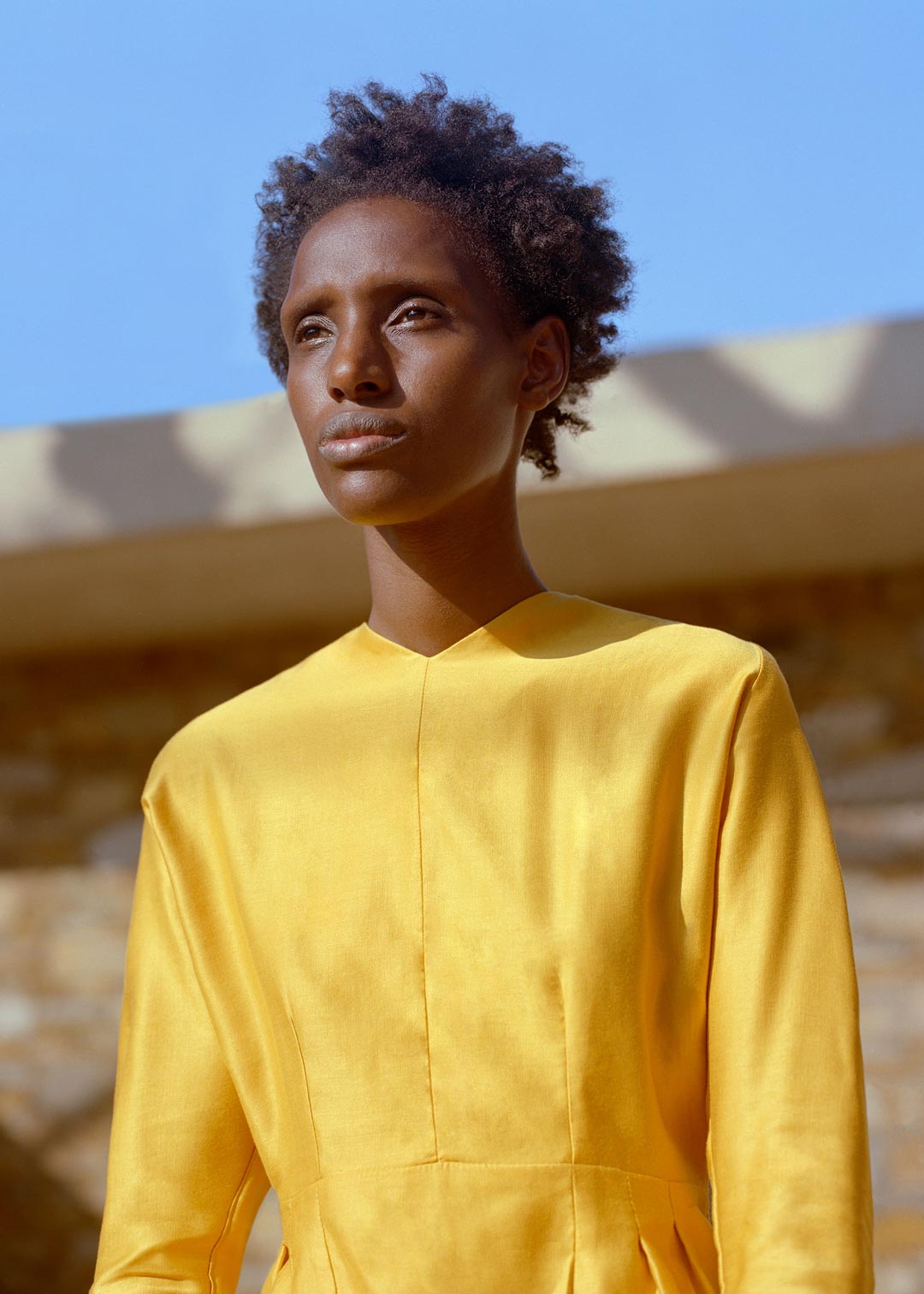
At this time, we had around 20 metres of an antique French silk from Lyon and really liked it, but we didn’t know what to do with it. Because of its shiny and ivory shade, it looked more like fabric for a wedding dress than fabric for an AZUR garment.
When we found out that these two women could pleat silk, we thought it could look very cool especially with this fabric. We made different tests and we absolutely loved the result of the hand pleated technique, which is not as geometrical as the other pleating styles. That’s how we decided to make a silk top and a dress in a very simple rectangle shape.
We started experimenting with beads for another project we have in mind, and we then saw that we could make necklaces out of them.
I’ve seen on your Instagram profile that you’re currently making beaded necklaces.
Yes! We were working on the new collection for this summer and, suddenly, the lockdown happened. As we have lots of antique beads, which we purchased over the last two years, we spontaneously decided to bring them with us in order to work remotely.
As we can’t make any clothes at the moment — because our seamstress is not at her studio — we decided to use these beads to make things we never find the time for. We started experimenting with them for another project we have in mind, and we then saw that we could make nice necklaces out of them. They are also used in our beaded bags.
And let me finish by saying that this is, again, another great example of constraints influencing your design process.
Well, there were higher forces at work this time. It kind of happened without thinking too much about it but, I guess it is! [Laughs]
1. When researching about French linen, Lisa and Lisa found out that it was often grown in France, sent to China to be woven and then returned to their home country.
2. Amongst the repair services offered by Azur, customers can have their garments re-waxed and re-pleated. Not surprisingly — considering the label’s location — a bottle of homemade Savon de Marseille soap is included in each order to be used for the first wash.
3. Also known as Tagua nut or ‘vegetable ivory’, corozo is a seed that comes from rainforest trees in South America and is collected after falling naturally.
4. leboncoin is a French classified advertisements website founded in 2006. A quick browse through its categories showed “voitures” (cars), “consoles & jeux vidéo” (game consoles & video games) and “montres & bijoux” (watches & jewellery).